Choosing the Right Plastic Resin For Injection Molded Plastic Parts
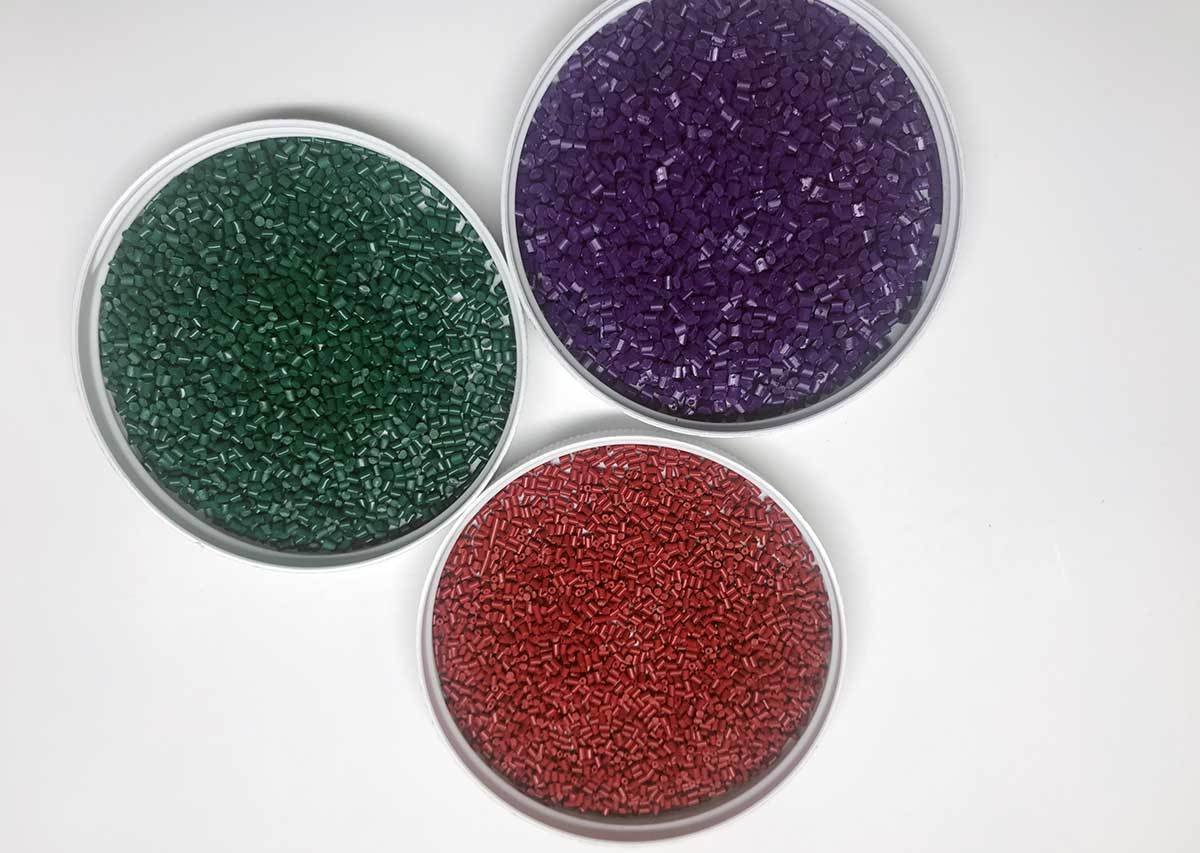
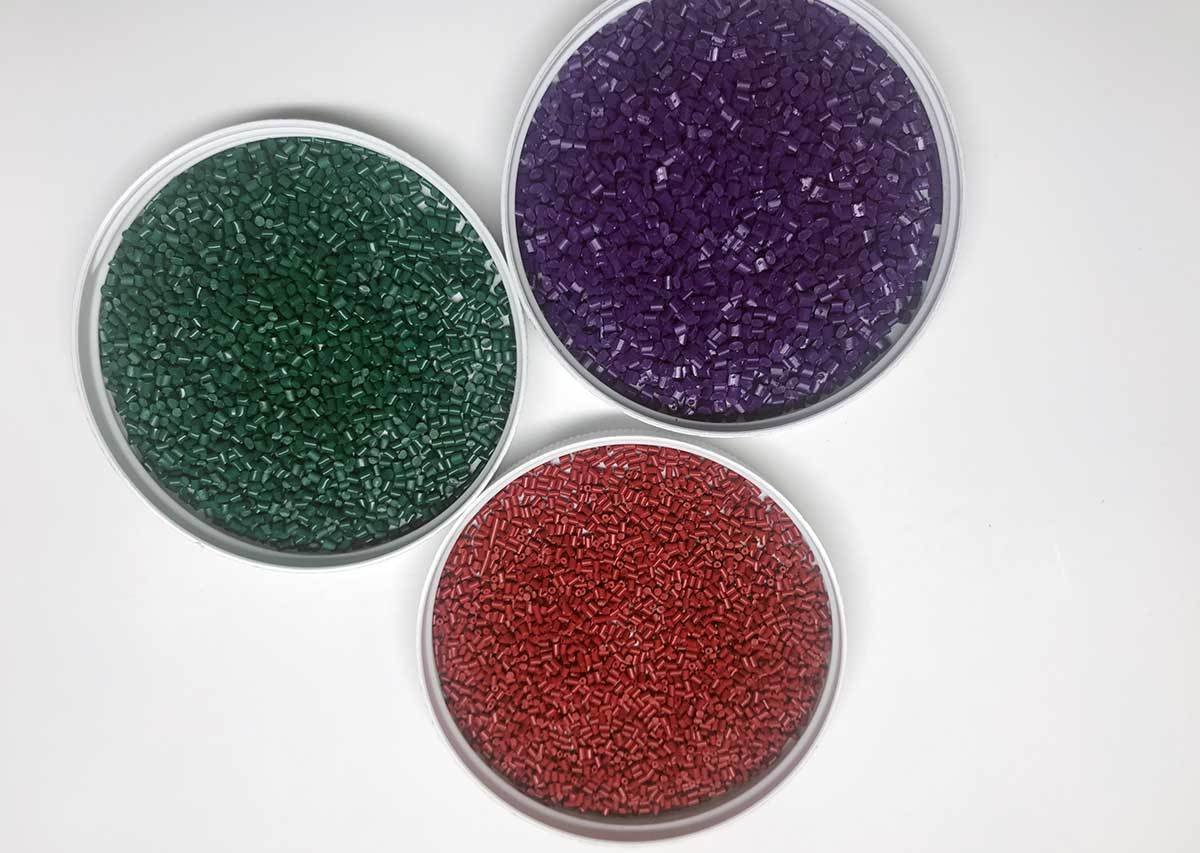
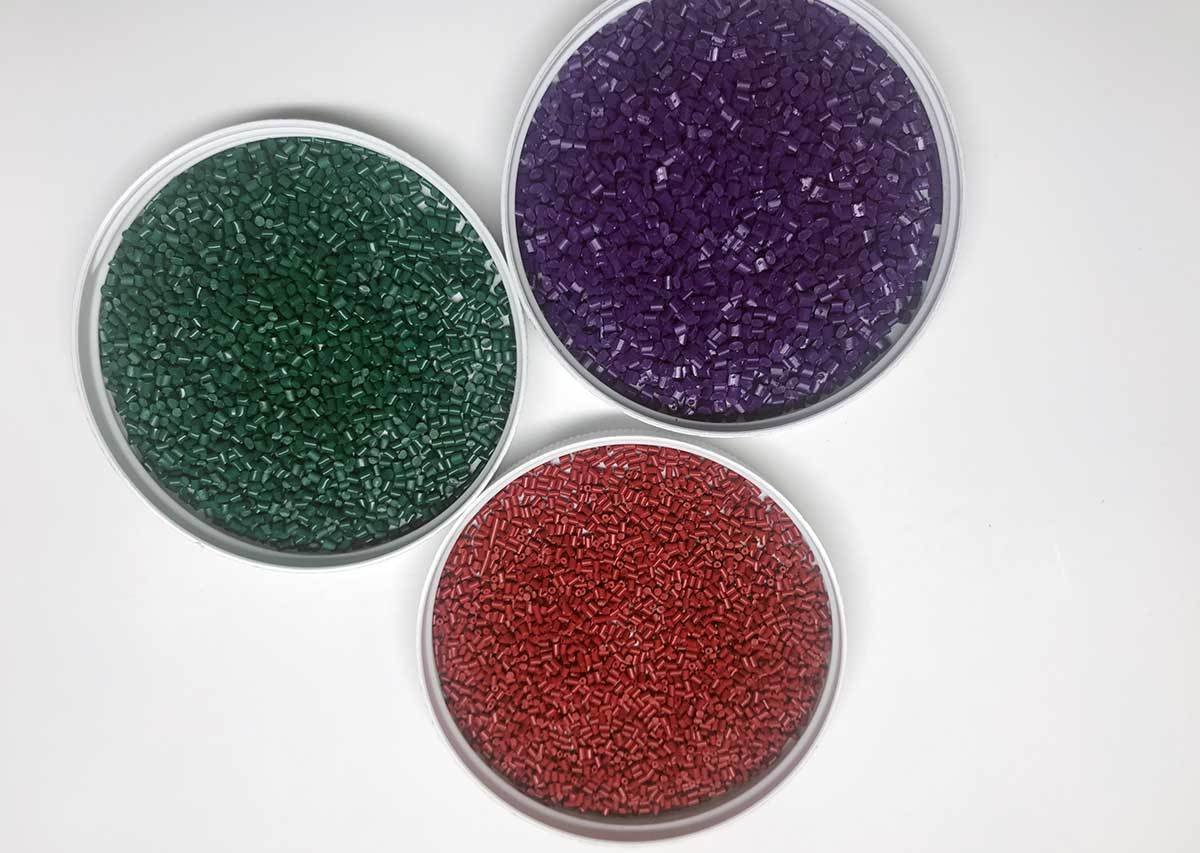
When it comes to choosing the right resin for your plastic injection molding project, there are a number of considerations that should be kept in mind. After all, different plastic resins and materials have different properties that can (and often do) influence the performance of a part.
The first and most important question to ask in a fundamental part assessment is: What is the application of the part to be injection molded? What will it do and how should it ultimately function? The below considerations are addressing this fundamental question. For example, you have made a shiny plastic part. When we ask what is the purpose of this part, your simple answer is a plastic case for a dental appliance. The below considerations explore of all the scenarios, expectations and possible future needs and options you anticipate for your plastic part.
There are several considerations to review before making the final selection on which plastic resin works best for your part. Plastic resins come in many varieties and there may be additives available to help you meet specific needs. There are commodity resins and engineering resins. The choices can be endless from a very common ABS plastic to TPE a plastic material that looks and acts more like silicone than plastic.
This article will review the most important considerations that you should keep in mind when deciding which plastic resin would work best for your project.
Some key considerations in deciding the right plastic resin to use for your injection molding project include:
- Will your plastic product be exposed to temperature variation?
- Will your plastic product be disposable or be used over a long life?
- Is your plastic part more functional or aesthetic requirements such as a high gloss finish?
- Does the product need to be made from a flexible plastic or a more rigid plastic?
- What plastic product regulatory requirements have to be met?
- Is the part functional or strictly aesthetic?
- Will the plastic part be required to withstand a specific mechanical or physical load?
- What is the best plastic resin for medical use?
Let’s review each of these factors.
1. Will your plastic product be exposed to temperature variation?
There are a few reasons that temperature variation will come into play in impact your resin selection, largely tied to the environment your part will be used in and the purpose that it will fulfill.
For example, if the product is for use outdoors, it may need to be able to withstand both heat and cold temperatures without compromising its integrity. There are products that are for use with applied heat or cooling.
Nylon, for instance, provides excellent thermal resistance, making it an ideal engineering grade to choose from for a product that will withstand demanding performance needs.
If you’re creating something that only needs to weather common environmental or household conditions, you might choose a commodity grade like ABS, which is weather resistant but can be damaged with extreme conditions. If you’re making something that’s unlikely to see extreme conditions in use, that wouldn’t be a concern.
2. Will your plastic product be disposable or be used over a long life?
Another consideration in your material choice is the lifespan of the product. If you’re creating a part that works inside of a mechanical setting—for instance, medical grade equipment—there’s a definite need to make sure that the durability of the material matches the purpose of the product. However, you wouldn’t need to create such durability for a piece that will be used in packaging, such as disposable water bottles or casings for consumer goods which will be thrown away when the product is finished.
The balance point here is in using the right material for the right purpose. You want disposable goods to be easy to recycle. You also don’t want them to cost more in production than they’re worth in price point. On the flip side, you need your long life goods to withstand the environment they’re created to perform in.
If you were making a food container that’s disposable, you might choose something like Polypropylene because it’s a lower-cost material that will work for your purpose. But if you were making medical grade products, you may look at lower grade engineering resins such as PC(Polycarbonate), POM(Acetal ) or PET(Polyester) or a higher grade engineering resin PEEK(Polyether ether ketone) might be a more appropriate material because the strength of this resin is very high and you can sterilize it, which is obviously important in the medical field. It’s also quite a bit more costly than materials like ABS, but that cost is necessary for the product.
3. Is your plastic part more functional or are there color requirements/aesthetic requirements such as a high gloss?
Some parts are simply functional and not seen by the consumer such as the inside of car versus other parts are mainly for aesthetic such as a faceplate for a wall switch. This is a determining factor for the deciding which type of resin would work best.
Color matching might seem like a small portion of the process, but many products are made for consumption by consumers, and this means that consumer appeal is important. Ultimately, this can make color and aesthetics a big concern, especially in areas where consumers will use these products for a long time.
An important consideration when thinking about color and plastic choice is: what is the use of the product? In some cases, parts that go into larger mechanisms may not need a wide color variety. In these cases, you can likely let other factors—such as strength, durability, and cost—influence your decision more than the color capabilities of a plastic.
In other cases, though, color and other aesthetic elements may be of greater concern. Resins used for car interiors, toys, and other products that people purchase for the visual appeal will need careful consideration aesthetically such as in regards to texture or high polish. Texture and high polish would also reference back to mold cavity specifications – not just the raw material. The plastic you choose in these cases will need to be a balance between performance factors as well as aesthetic elements such as a particular plastic’s color-lasting or matching capabilities.
4. Does the product need to be more of flexible plastic part or more of a rigid plastic part?
Flexibility and rigidity requirements are also important factors to take into consideration when choosing a plastic for your project. This requirement will often be considered along with the strength of the product—does it need to replace a machined or die-cast metal part in a machine? Will it be load bearing? Does rigidity compromise its lifespan or add to the lifespan?
Some resins, such as Polycarbonate (Lexan), are naturally more rigid than others. Some, such as Polyethylene, are more flexible and may work better for your flexible injection molded part. Some, like PVC, might be made rigid for certain uses and flexible for other uses.
5. What plastic product regulatory requirements must be met?
Almost any industry you might create a part or product to accommodate has its own regulatory requirements that you will need to meet. These requirements are integral to the creation of your products.
Regulatory needs may vary, but it’s important to research individual compliance issues before choosing your resin. Of special importance will be requirements around durability and strength, depending on the end use of the product or part.
Some regulatory bodies you may need to work with include: The FAA, FDA, REACH, NSA, and the EPA.
6. Will the plastic part be required to withstand a specific mechanical or physical load?
It is important to look at properties of a resin such as impact and strength for those plastic parts whose primary purpose is for function versus aesthetic.
These parts include parts inside your printer, under-the-hood automotive applications, or motor brackets for example. Some plastics inherently handle mechanical or physical load better than others and, in some cases, there are additives to assist in meeting load or strength requirements. See our reference tables for density values and abbreviations for common resins.
7. What is the best plastic for medical use?
Selecting the appropriate plastic resin for medical devices is crucial, and one of the top choices is often polyethylene or polypropylene. These materials are known for their biocompatibility, meaning they have minimal risk of causing an immune response or adverse reactions when in contact with living tissues. Additionally, both polyethylene and polypropylene are lightweight, durable, and possess excellent chemical resistance, making them suitable for a wide range of medical injection molding applications.
Medical-grade polyethylene is commonly used in applications like orthopedic implants, while polypropylene is favored for devices requiring flexibility and clarity. These resins meet stringent regulatory standards for medical devices and contribute to the production of safe and effective healthcare products. As always, the specific requirements of the medical device and the intended use should guide the selection of the most suitable plastic resin.
Weighing All of Your Options
Ultimately, choosing the right plastic resin for your plastic injection molding project will come down to balancing multiple considerations against others.
How does your need for strength and durability balance against your budget? How does your desire for certain aesthetic qualities balance against performance needs? Etc. Answering these questions can help you settle on the best plastic for your particular needs.