Hot Runner and Cold Runner Systems for Plastic Injection Molding
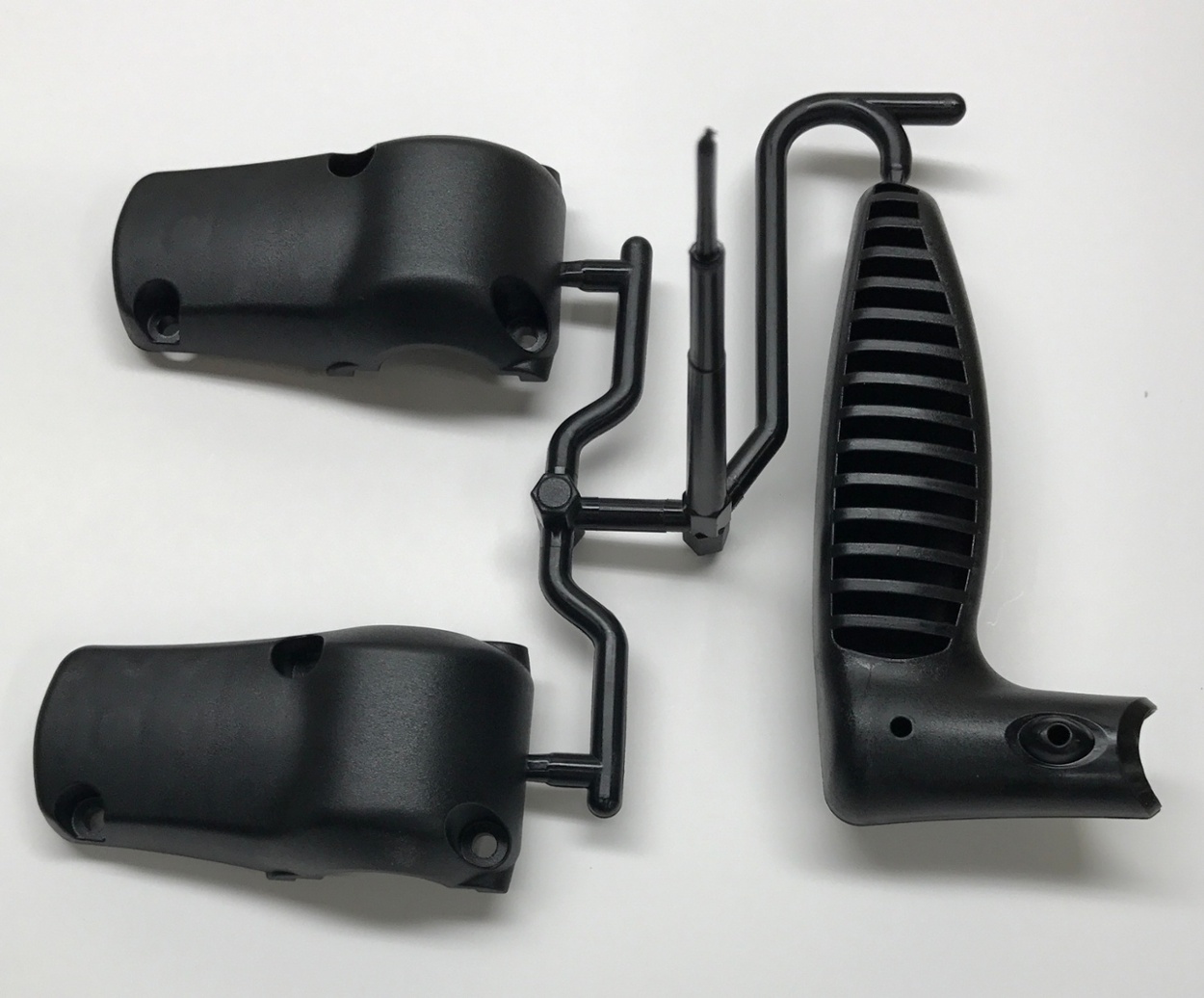
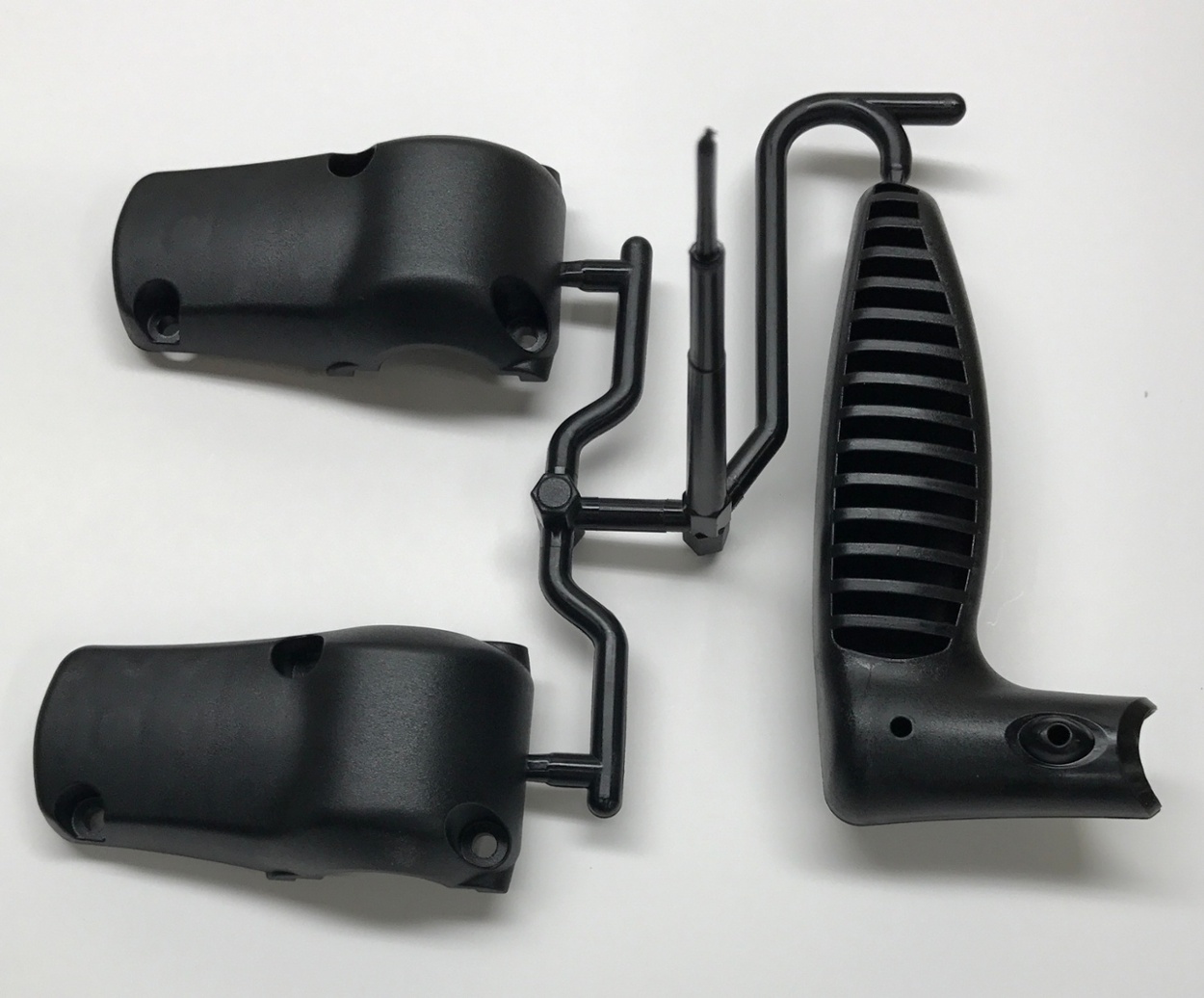
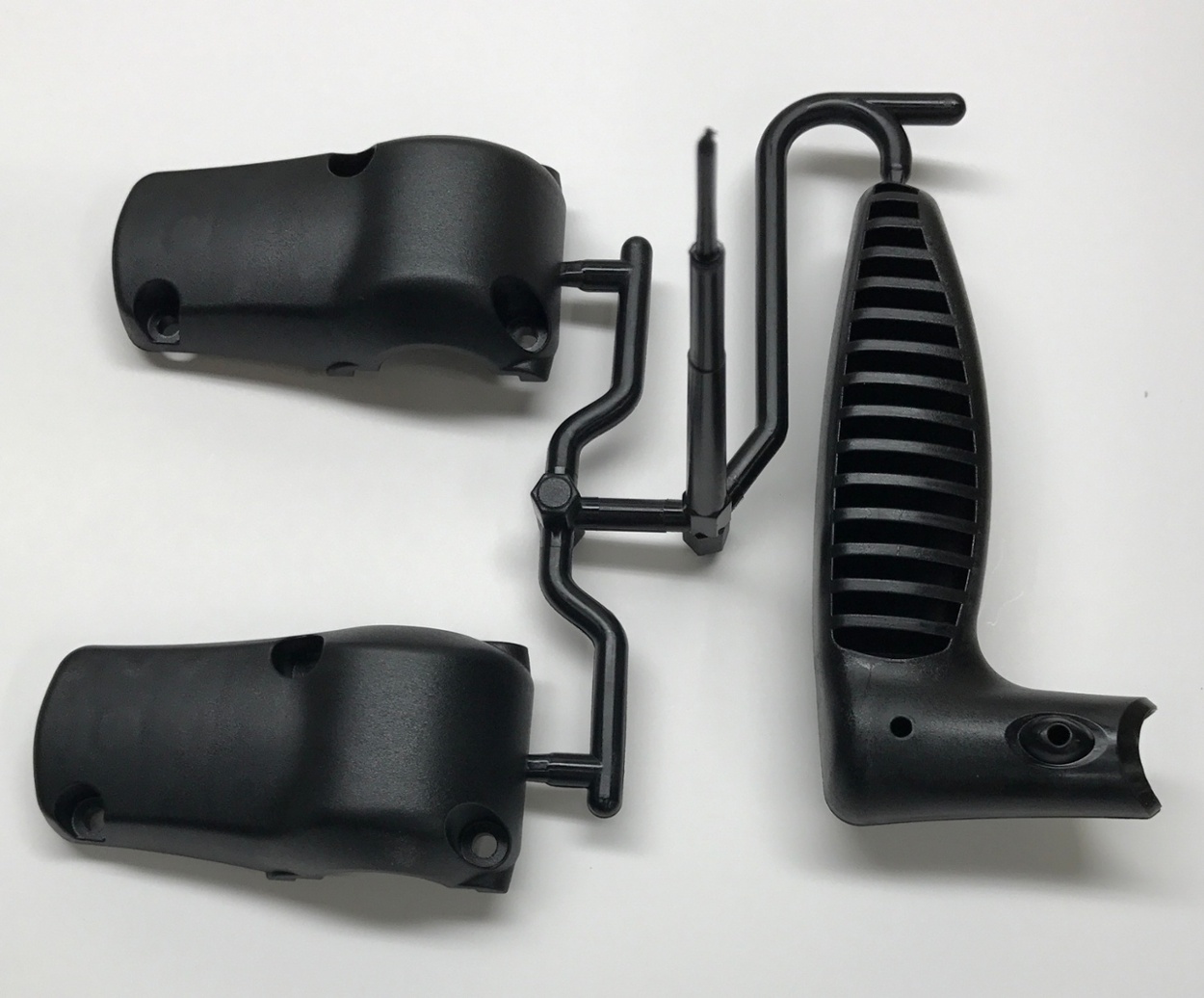
The use of hot runner systems in plastic injection molding has been possible for nearly 50 years, but it’s only since the late 1990s that the use of a hot runner system surpassed cold runner systems in plastic injection molding.
In a hot runner system, a manifold system heats the mold tool and sends melted plastic to nozzles which deliver the plastic to various cavities within the mold. Hot runners may be either internally or externally heated. External hot runner systems are excellent for use with polymers that may be sensitive to temperature fluctuations, but internally heated systems offer better flow control.
In a cold runner system, the plastic injection occurs through the sprue. The plastic fills the runners leading to the cavity. Both hot and cold runner systems have advantages and disadvantages that may make one system more applicable to a certain plastic injection molding use case. Here’s a look at the pros and cons of each.
Hot Runner System in plastic injection molding
Advantages
- Eliminates runners and material waste
- Can assist in even melt flow
- Faster cycle times
- Assists with post mold automation processes
Disadvantages
- Higher maintenance costs
- More potential downtime
- Higher tooling costs
- Slower color changes
- Not suitable for thermal sensitivity materials
- Higher molded part production volume to pay for higher mold costs
Cold Runner System in plastic injection molding
Advantages
- Can accommodate a wide variety of polymers, including specialty polymers
- Quick color changes
Disadvantages
- Slower cycle times than hot runner systems
- Creates more waste from runners
Deciding Between Hot and Cold Runner System for Plastic Injection Molding
Since the cold runner system wastes the plastic that fills the runner, it may not be the best choice if the job calls for an expensive specialty plastic. If the product won’t be used in food or a medical device, scrap from the runner can often be reground and reused. However, the regrinding process is expensive in itself, as well as noisy and dirty. In most applications, the proportions of new to reground materials are strictly controlled, which can lead to a build-up of unusable material.
With hot runner injection molding, there is little or no scrap, eliminating this additional cost.
Hot runner systems often have faster cycle times, which reduces processing costs. They will also produce less wear and tear on the equipment, helping to increase uptime and reduce maintenance costs. The ability to design mold channels to ensure that the material flows the same distance from each nozzle helps improve quality by moderating pressure and thermal variations This may be extremely important with certain resins that have limited processing margins.
In addition to the speed, product quality and resin characteristics of the job, it makes sense to consider other factors that can affect overall costs. Consider the availability of engineering and design assistance that the supplier may provide to help you get the most from the system you choose. Also consider service costs—cold runner systems may be more reliable because of their simplicity.